This making salad bowl project is approximately 8″ in diameter by 4″ high, however, any size of block can be used. This salad bowl has some unique design features. First, there’s a decorative textured band just below the rim.
Second, there’s a slight undercut inside the top of the rim to allow the bowl to be picked up more easily and to help direct the salad leaves back into the bowl rather than onto the table. In case you need the best salad bowls, we have recommendation for you.
DIY Salad Bowl Step-by-step
Preparing the Blank
This salad bowl is made from an 8-1/2″ diameter by 4-1/2″ round disk. The first step is to decide the best grain pattern in the blank. Select and mark the side that will be the top of the bowl. Put a dimple at the center of the block on both sides. Drill a perpendicular hole in the center of the top suitable for a woodworm-type screw mount for your chuck. A drill press is best for this. I drilled a 5/16″ × 1″-deep hole to fit the Woodworm screw in my Super Nova chuck. Check your chuck’s requirements, as each manufacturer is different.
Mount the chuck on the lathe spindle, and twist the blank onto the screw chuck until the face seats firmly against the chuck jaws. If you don’t have a chuck, you can center the blank on a faceplate and modify the mounting procedure to suit.
Shaping the Outside Surface and Base of the Salad Bowl
Position the tool rest at a 45° angle to the lathe ways and about 1/4″ from the highest point of the blank’s corner. Adjust the height so that a 1/2″ bowl gouge will cut the lathe’s centerline.
The tailstock should be raised for support, the clamp tightened and locked in place, and the blank should be spun to avoid hitting the tool rest. Shape the outside surface of the bowl at a slow speed (around 500 RPM) if the tool rest is not closely aligned with the blank’s cutting surface.
When you follow the wood grain from the narrow diameter of the blank to the wide diameter, you can reduce tear-out. Clapham’s sanding and cutting compound reduces tearout by softening wood fibers in a blank with an uneven grain pattern. To date, this product hasn’t caused any problems with the final finish.
When the vibration level decreases, you can increase the lathe speed. A smoother surface allows for faster wood removal, making sanding easier as a result of faster speeds.
It is necessary to tenon the tailstock end to make it fit the chuck. For some chucks, straight-sided tenons are required. A dovetailed tenon is required for others, such as the Nova chucks I use. Tenons should be long enough for the tips of the chuck jaws to rest on top of the bowl at the base, and should not touch the inside bottom of the jaws. It is possible to hold a bowl blank more firmly and accurately with this method.
You use the Woodworm screw by removing the bowl from it and reversing it into the jaws of the chuck. When the blank is reversed, there will probably be a little wobble since it is nearly impossible to remount the blank perfectly. True up the outside surface to reduce vibration. Fill in the blank with the correct information.
Reduce the lathe speed to about 500 RPM, and finish sand the outside surface. With an angle power drill/sander, I usually sand with 4″-diameter disks on a 3″-diameter sanding pad with a sponge spacer. I start at 80-grit to remove the tool marks, and work my way up to 320-grit, and then hand sand with 400- or 600-grit. Hand sanding the entire outside surface will also work; it just takes longer.
Making The Textured Band
The textured band should be applied before hollowing out the inside, as the walls have not been turned and will not flex. Approximately 3/4″ wide, the texture band on this bowl extends from the top of the rim to 3/4″ down. On the bowl surface, mark the location of the band’s edges. Make two small grooves where the marks are. Place the tool rest 1/4″ from the surface and skew it so a skew cuts on center.
Use a texturing tool to create a texture pattern between the two grooves. I used a Robert Sorby Spiraling/Texturing tool with a 1-1/2″-diameter texturing cutter. The adjustable tool saddle was positioned 90° to the cutter. Position the tool rest so about 3″ from the bowl’s surface. Place the texturing tool on the tool rest so it can be pivoted up to create the texturing design.
The texturing cutter should contact the bowl surface just below the center axis to avoid a catch. Adjust the lathe speed to about 500 RPM and press the tool against the wood between the grooves. Use different cutter wheels and settings to create the texture design you want.
In order to color the textured band later, you must seal the grooves in the wood pores so the dye won’t leak through. For this purpose, you should burn the grooves with a wire wood-burning tool.
If the wire tool is very hot, it is easy to burn your fingers, so do not wrap it around your fingers during this process. If a hot spark is generated during this process, turn off the dust collector.
Hold the wire burning tool in the grooves until the wood is charred. This only takes a few seconds. After the grooves have been charred, burnish the textured area with shavings to remove any fuzz. The band is now ready for finishing.
You need to paint the band, not stain, so that the color penetrates well into the wood. Acid dyes are best, but aniline dyes can also be used. Apply the dye carefully as you turn the bowl. A mark outside the band is very difficult to remove.
Forming the Inside Surface of the Salad Bowl
Drilling a depth hole 1/4″ – 1/2″ smaller than the finished depth measurement is a good option. I use a 3/8″ long shank drill bit set in a handle to do this. The tool rest can be positioned to provide a center-aligned bit. With masking tape, mark the appropriate depth on the bit shank, line the bit with the lathe ways, and drill straight into the blank at a slow lathe speed (around 250 RPM). Clear the flutes as needed until you reach the appropriate depth.
Adjust the tool rest height so the 1/2″ bowl gouge can cut straight through the center line. Begin cutting with the gouge set at 90 degrees to the tool rest, and cut towards the center with the bevel rubbing. Cutting in this direction helps to decrease tear-out by allowing the cut to follow the direction of the wood grain. You can utilize a curved tool rest to reduce the gouge’s extension over the tool rest if you have one. Continue to make lengthy, sweeping cuts that follow the outside surface’s shape. To make the cuts a little more forceful and remove the wood a little faster, gradually rotate the gouge to around 45°.
Calipers should be used to measure wall thickness frequently. Double-ended calipers let you see the wall thickness immediately on their outside ends. Near the rim of the bowl, undercut just below the top of the inside wall as you get closer to the completed bowl wall thickness.
When you reach the bottom of the bowl, you will notice that the bottom of the depth hole disappears, indicating the bowl bottom is close. If you switch to a bowl gouge with a steeper bevel, it is easier to get a good cut on the bottom surface because you can continue to rub the bevel. In addition, this will ensure you have enough wood to form the outside of the base. Keep track of the depth of the bowl by using a depth-measuring tool. To find the inside bottom of the bowl, align the measuring tool across the rim, then sight along its end to see where the measurement falls.
The bottom of the bowl should be a little thicker than the walls to make it more stable in use. I often shear scrape the surface with a large side scraper to make it smoother. Make the rim crisp but not sharp. Sand the inside surface as I described earlier, using sanding disks and a sponge spacer to allow the sandpaper to conform to the inside surface without digging into it.
Completing the Base
When the bowl is sanded to your satisfaction, remove the tenon and complete the base. The bowl needs to be reversed and mounted with the bottom exposed. There are various ways to mount the bowl. In this project, I used Cole jaws mounted on the chuck.
Remove the bowl from the chuck, and set the depth gauge at the inside depth of the bowl. This will help you determine the location of the inside bottom as the base is being turned.
You can mount a bowl in Cole jaws in compression or expansion mode. When setting up to hold the bowl in expansion mode, make sure the bowl is pressed securely against the chuck to ensure maximum holding strength.
Make sure the bowl does not hit anything by placing the tool rest about 1/4″ away from the bottom surface and spinning the lathe. Chucks with Cole jaws attached are designed for lathe speeds up to 600 RPM. Turn the lathe at a very slow speed.
The speed should be gradually increased. By using a very light cut on the tenon while using a sharp 1/2″ bowl gouge.
Using the depth gauge, measure the thickness of the bottom of the bowl. You want the bottom of the bowl to be a bit thicker than the wall to increase the bowl’s stability. This will prevent the bowl from wobbling on a table.
I like to engrave my signature on my bowl while it’s still on the lathe, so I can remove any fuzz created by the engraver before finishing the bowl. Sand the base to 400- or 600-grit and add any decorative rings.
Finishing
Finishing bowls can be done using a variety of materials. I like to use three to five coats of curing oil to complete my salad bowls off the lathe. The number of coatings required is determined by the wood’s absorption quality and the desired level of surface finish.
As the wood cures, a curing oil penetrates the surface of the bowl, leaving a little deposit on the surface and sealing the wood. Salad oils, for example, are prevented from soaking through and becoming rancid. Tung oil, walnut oil, linseed oil, and proprietary mixtures of these are examples of curing oils. I generally use a Danish oil made primarily of linseed oil. Non-curing oils, such as vegetable, mineral, and other non-curing oils, never cure, and some can go rancid after a while.
Flood the surfaces with oil and allow it to soak in. Wipe away any extra oil after a few minutes and let the bowl dry for a few hours. Apply subsequent layers in the same manner, allowing the previous one to cure until no odor is detectable. This could take several weeks. If desired, the final polish can be rubbed.
To create a lustrous surface, some turners like to employ a polyurethane finish. These produce a film-like surface, which I find unsatisfactory because they crack and peel off easily and are difficult to restore.
After the finish has dried, your lovely salad bowl is ready to serve at the dinner table with your favorite tossed salad.
Was this helpful?
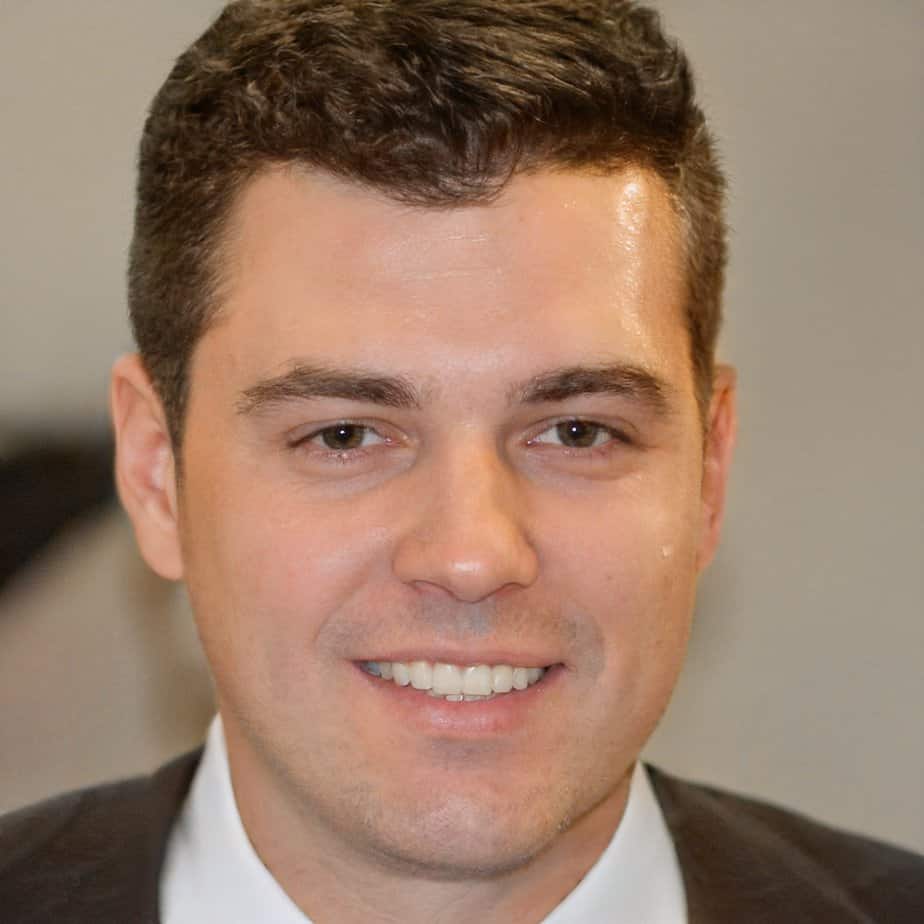
Hi there! I’m a food enthusiast and journalist, and I have a real passion for food that goes beyond the kitchen. I love my dream job and I’m lucky enough to be able to share my knowledge with readers of several large media outlets. My specialty is writing engaging food-related content, and I take pride in being able to connect with my audience. I’m known for my creativity in the kitchen, and I’m confident that I can be the perfect guide for anyone looking to take their culinary journey to the next level.