DIY Honey dipper, make your own honey dipper, is that possible? A Honey Dipper is a pleasant and simple product to keep on hand. The purpose of this tool is, they remove liquid honey from jars and allow you to drizzle it into your tea or on toast. Honey dippers are a terrific addition to your inventory because they don’t require any additional hardware or precision turning.
Honey Dipper
The Honey Dipper is a device that is used to regulate the flow of liquid honey. The slotted holes allow you to take up a lot of honey, and you can regulate how much is in your tea or on your toast by rotating the dipper. The amount of honey taken up is affected by the form of the dipping end. They’re a fun project to turn. In case you need a recommendation for the best honey dipper, we have a list for you!
DIY Honey Dipper: Materials & Tools
You can use little branches or cut the wood into 1” squares on your table saw if it’s just under an inch in diameter. To keep your fingertips safe, make sure you utilize the right safety gear. This is a fantastic way to use local wood, such as neighbor’s cuts or native species. Honey dippers were made from Jack Pine, Larch, and Birch, all of which were discovered on my property. I would avoid using greasy wood because it could taint the honey. Toxic wood should not be used. The following image displays finished dippers, a larch branch, and three dogwood turning blanks, one of which has been turned around and is ready to use.
DIY Honey Dipper: Tools Needed
- Roughing gouge – to turn the blank round
- Parting tool – to cut grooves in the dipper
- Skew Chisel or Spindle Gouge – to shape the dipper and handle
- Sand Paper – various grits (I used 150, 220, 320, 400, 600, and 800)
- Cotton cloth or paper towel – to wipe the dipper off between grits
- Food Grade finish
When you’re finished, you can turn the honey dipper entirely between centers with only a little cleanup at each end. I utilized a multiple jaw chuck to hold the blank, which allows me to finish the dipper’s handle end entirely (see pic below). This product is ideal for production runs when the blank is initially rounded and a tenon is added before moving to the multiple jaw chuck for shaping. With a little practice, you can turn out two or three in an hour if your tools are sharp. If you’re using exotic wood that you had to buy, raise your prices. Dippers should use locally sourced or found wood. When deciding on a price, make sure it accounts for your turnaround time.
Occasionally, a fault in the wood surfaces during the finishing process. On my larch, I noticed fractures and insect damage. In any case, finish the honey dipper. You can utilize it as a demo product or place it in a clearance bin. Throw it aside unless it is harmful to use or may break too readily. In certain cases, the imperfection adds to the product’s personality. So think twice before discarding your less-than-perfect turns.
DIY Honey Dipper: Turning a Honey Dipper
I began by turning the prepped dogwood blank round and making a tenon to fit into the chuck. The completed dipper illustrates where the key features are located.
Mark the approximate locations of the dipper and the tapered parts of the handle with a pencil. I also label the parts on the end so that separating the dipper off the lathe is easy. With the separating tool, I first trimmed the ends. After that, I fashioned the honey dipper’s dipper end. If you like, you can cut the grooves first and then shape.
Make the grooves in the dipper using a knife. When I’m doing this, I prefer to gaze down on the dipper so that I can line up the depth of each groove and keep it consistent. If your parting tool is burning the wood, check to see if the tip is the same width (or smaller) as the body. To prevent friction on the wood, your parting tool should have a tip that is somewhat larger than the blade.
Toss the handle about until it’s the right shape for you. Create an appealing top for the handle by defining the dipper end.
DIY Honey Dipper: Finishing Your Honey Dipper
The honey dipper’s body should be sanded and finished. Depending on how smooth I was able to form the spindle, I use progressive sand paper ranging from 150 to 220 grit. I wipe off the turning with a cotton cloth or a paper towel after each grit change. This eliminates any grit that may have dropped off your sand paper and protects your work from being scratched by a higher grit.
Was this helpful?
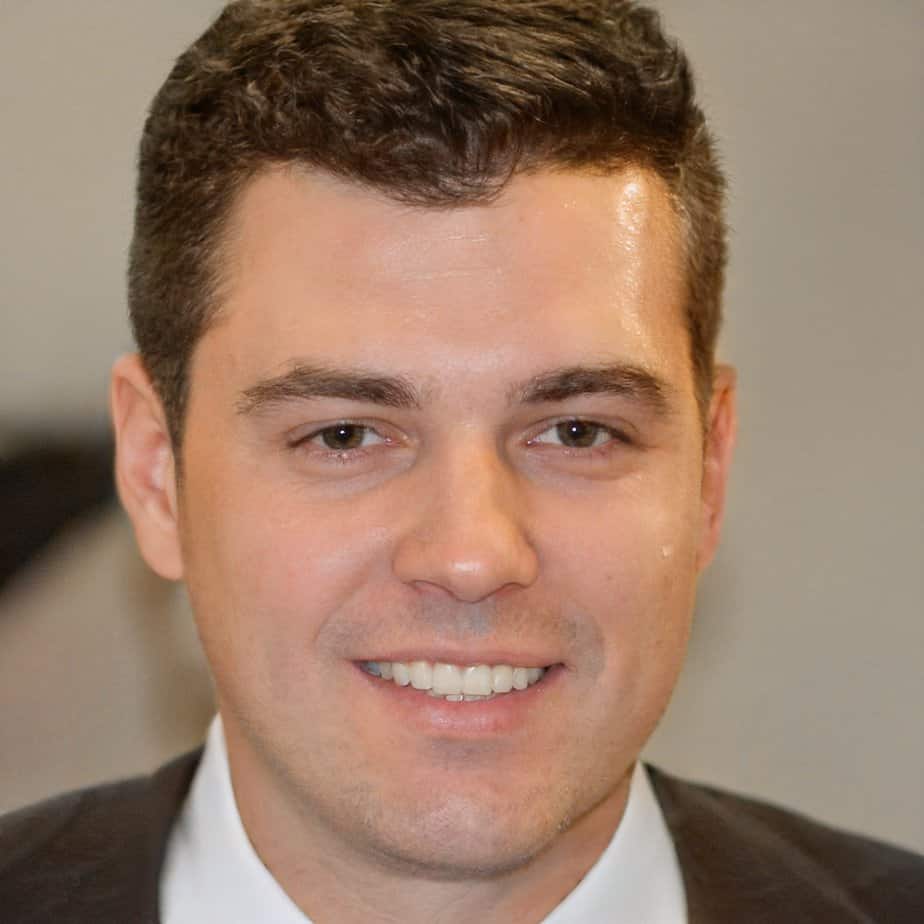
Hi there! I’m a food enthusiast and journalist, and I have a real passion for food that goes beyond the kitchen. I love my dream job and I’m lucky enough to be able to share my knowledge with readers of several large media outlets. My specialty is writing engaging food-related content, and I take pride in being able to connect with my audience. I’m known for my creativity in the kitchen, and I’m confident that I can be the perfect guide for anyone looking to take their culinary journey to the next level.